One less known peculiarity of modern reflector type telescopes with aperture larger than approximately 40 cm is that they should never be tilted close to the horizon. The reason for this is quite simple - large primary mirrors are usually not firmly fixed to the telescope frame but are instead left “floating” inside a mechanical, hydraulic or pneumatic “cell”.
On the positive side, this technique enables premium quality mirrors to form perfect optical images without distortions caused by bolting them onto the framework. On the negative side, this makes telescopes highly vulnerable to accidental misuse - should one tilt the telescope into a horizontal position, the primary mirror may either shake inside the cell, which would demand immediate repeating of the touchy calibrating procedure, or it may actually completely fall out of the apparatus, which would create a sudden vacancy in junior researcher positions.
The purpose of the device described in this article is to sense tilting of the apparatus by more than a strictly predefined number of degrees of arch away from the vertical axis. If sensor is tilted for more than e.g. 75° from the vertical, it trips and stops further motion of the valuable peace of equipment. One might argue that such sensors already exist - there are for example inexpensive mercury tilt switches at the market. This is of course truth but the case is not quite as simple as it may seem at first.
Off the shelf solutions
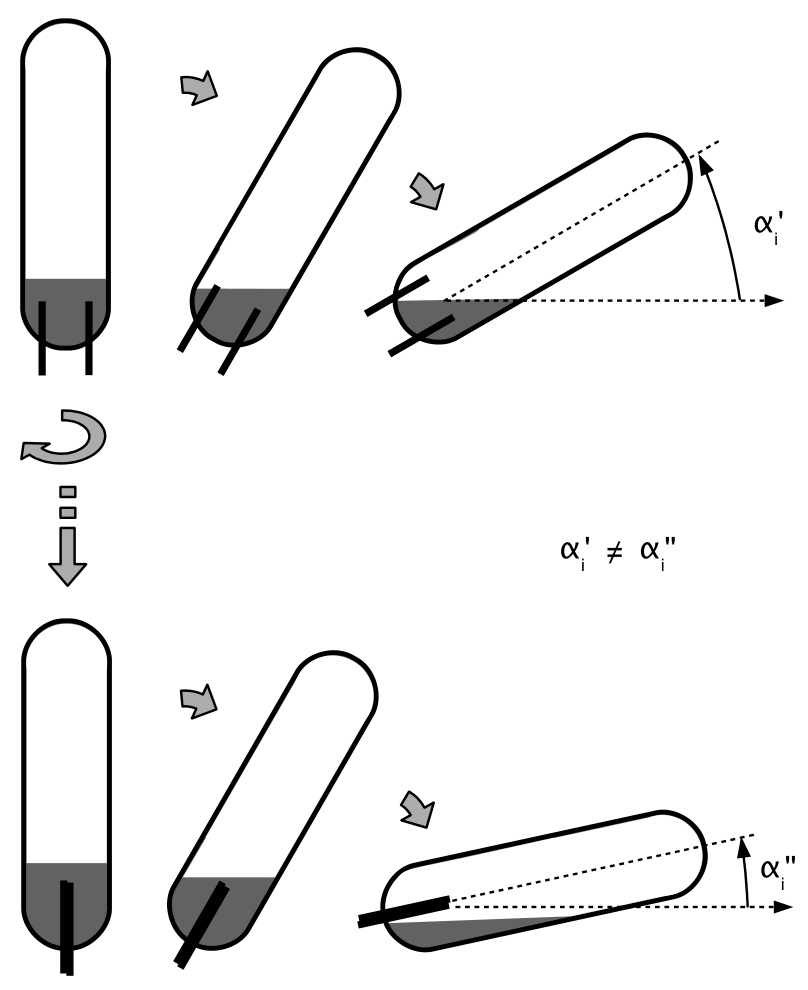
Let’s consider mercury tilt switches. They are usually made in the form of a glass capsule half filled with metallic mercury, with two metallic contacts welded into the bottom of the glass housing. If such sensor is tilted, mercury inside it flows away from the bottom and breaks electrical contact between the two protruding wires. Unfortunately mercury is a highly toxic substance and all sorts of electronic components containing it are being taken out of the market for good. But the more important fault of mercury sensors having in mind the potential use in astronomy is that they do not react equally well to the same vertical tilting angle at varying azimuth angles. The cause of this is rooted in the very construction of such sensors - since there are two parallel wires inside the capsule, electrical contact gets established (or discontinued) at noticeably different tilting angles if vertical sensor is for example simply tilted down or firstly rotated in horizontal plane for 90° and then tilted down. In one case its two internal wires might be positioned parallel to each other in vertical-, while in the other case they would be positioned parallel to each other in horizontal plane when the sensor becomes eventually brought close to the horizontal position. The next diagram illustrates the problem.
Component data sheets confirm this too well. Tilting angle dependence on the azimuth is as high as 15° for certain models. It stands to reason to assume that no astronomer would be happy to operate a telescope limited to inclination angles higher than +15° when looking towards e.g. north or south, but to unacceptably high +30° when looking towards east or west.
Other sensor technologies that have been taken into consideration included MEMS (Micro Electro-Mechanical Systems) off-the-shelf devices often used in car alarms and laptop computers, but sadly no such component suited telescope needs. For example, none could have been found with sufficiently large tilt angle, and none provided any means for users to adjust the tilt angle to the necessary value. There are also special hybrid accelerometer chips at the market able to sense the direction of the gravitational field, which can be used to calculate the actual inclination of the telescope using a microcontroller running a not so trivial algorithm. Although able to produce precise information, operating range of both types of sensors, as of time of planing the system, did not include temperatures below 0°C - but that was of course an absolute necessity remembering that the astronomical observatory is located at the very top of a mountain. Finally, the point well worth mentioning is that complicated high-tech solutions might not be especially appropriate for constructing the ultimately reliable equipment; if one wants it to act a a telescope life saver of the last resort, there should not be a lot of things that can go wrong inside the sensor itself.
So after quite a lot of thinking over and deep web digging, we decided to steer away from commercial gadgets and construct and build the tilt sensor with our own forces. We opted for a sturdy steam-engine, or at least that is what the sensor looks like from the outside...